When Designing Plastic Injection Molded Components, What You Should Pay More Attention to?
Plastic injection molding is the benefactor of a multitude of advantages. In large runs, molding is much cheaper than machining the parts individually. The manufacturing speed is also much faster.
It is also important to know that when designing a part that will be molded - there will be some special considerations that will need to be applied.
Plastic injection molded parts are created by injecting liquid plastics into mold cavities. This liquid is also injected over cores, which means they require draft in order to release from the mold.
Draft is the term used to describe the amount of taper on the vertical walls of the plastic part. Without draft, a part will either not eject from the mold - or it will sustain damage during ejection. Typically, draft angles between 1° and 2° are required. These also vary depending on part restrictions and specifications.
Designing Plastic Injection Molded Parts For Consistency
Plastic parts should always be designed with a nominal or consistent wall thickness. Every injection molded part shrinks as it cools and differences in the thickness of the part will cause the part to shrink at different rates.
Thicker areas of the part will shrink more than in those thinner areas. This has been known to result in the deformation of the part. Another issue is sink marks, which are areas of the part that are “dimpled” due to excessive shrinkage. The solution to this problem is to remove or “core out” thick areas of the part to avoid these conditions.
Part designs with nominal wall thicknesses may not be as strong as a thicker part. When this is the case, ribs are used for strength. When utilizing ribs on a part - their thicknesses should never be less than 70% of the nominal part thickness in order to avoid sink marks. As with other vertical surfaces on the part - the ribs should also have draft.
Plastic Injection Molded Part Designs
There are times when a receptacle for a screw or threaded insert is required on a plastic part. Design features like these are called bosses. Bosses are used when the part - is part of an assembly. These should be cored to the bottom in order to best maintain uniform wall thickness.
In a case where two halves of an injection mold separate in opposite directions, the features of the plastic injection molded part generally need to be able to release in that same direction.
For any of the part features such as holes, or undercuts, or shoulders, etc that cannot release in the direction of the mold separation - these will require either redesign or special attention.
Exceptions To The Rule
Any time the axis of a hole is formed in the injection molded part - it has to be parallel to the direction of mold separation. There are only a few exceptions to this rule.
When a hole whose axis is slightly angled from the direction of the mold separation - this can be crated with a “split pin” design, where half of the coring required to make the hole is on one side of the mold and the other half is on the opposite side.
It is also true that mold components called “side actions” are often used. This is done to pull coring in a direction other than the direction of mold separation. This design feature adds flexibility to the part design. It also increases the price of the mold.
When you have 3-D simulation software - it can really help a designer make critical decisions about the design long before the injection molded part is ever manufactured. Some of the most important items to consider include;
Gate locations, ie; how the injection molded part will fill
Determination of specific resin for application
Determine if the part has excessive shrinkage and warpage
Identify areas that may cause sink marks
There are other considerations as well for designing an efficient injection molded plastic part. Every part design is unique and the requirements and functions of the part will often make following these considerations a challenge.
To discover how to perfect this process - you can partner with Crescent Industries because their employee-owners have the experience, longevity and market expertise to help with your next injection molded project requirements. Click on Link below to Register to Receive Crescent Industries Injection Molded Part Design Guidelines.
19
2023-06
Scan the code and consult immediately
Follow usYou can follow us for more information
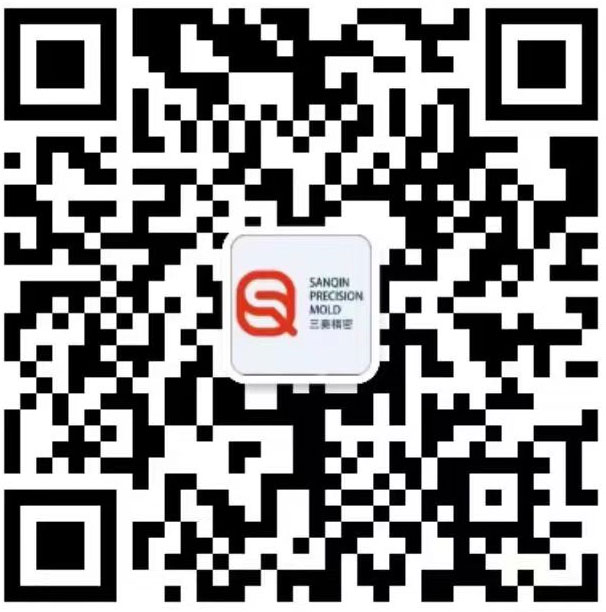
Sanqin Precision Mold
Official WeChat
